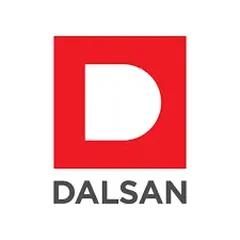
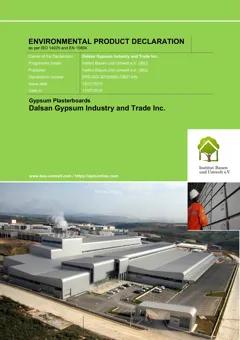
EPD: Gypsum plasterboard, 12.5 mm, 650-900 kg/m3, Dalsan
Discover the versatility of gypsum plasterboard, your ideal solution for creating durable interiors. With excellent insulation, easy installation, and a smooth finish, it’s perfect for walls and ceilings in residential and commercial spaces.
Gypsum plasterboard offers excellent thermal and acoustic insulation, lightweight design, and a smooth surface for finishing. It's easy to cut and handle, making it user-friendly for both professionals and DIY enthusiasts.
Gypsum plasterboard is applied to wal...
Manufacturer:
Dalsan
Group:
Country of production:
Product name:
Gypsum plasterboard
Category:
Gypsum and plaster
Class:
Regular gypsum board
Type:
Regular
Environmental impacts
Global Warming Potential (A1-A3):
1.98 kg CO2e/m²
Technical specification:
12.5 mm, 650-900 kg/m³
Available units for calculation:
m², kg, ton, m³
Unique identifier (OCLID):
594983f05d96ff5dc0910b2c
Sustainability data background information
EPD number:
EPD-DGI-20130062-CBD1-EN
EPD program:
IBU
Publication year:
2013
Product Category Rules (PCR):
PCR Plasterboard, 07/2012
Environmental standard:
EN15804+A1
Data source:
EPD Gypsum Plasterboards Dalsan Gypsum Industry and Trade Inc.
Verification status:
Third-party verified (as per ISO 14025)
Upstream database:
GaBi