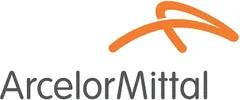
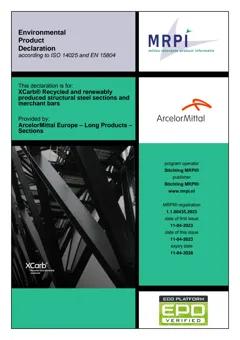
Other manufacturers with similar products
EPD: Recycled structural steel section made via EAF route made with reneweable electricity supply, 7850 kg/m3, XCarb®, ArcelorMittal Europe Œ Long Products Œ Sections
Discover XCarb®, the revolutionary recycled structural steel section made via EAF route with renewable electricity. Combining sustainability with superior performance, its lightweight yet strong design makes it a smart choice for eco-conscious builders seeking to minimize their carbon footprint.
This innovative structural steel section provides exceptional strength and durability while being environmentally friendly. Its sleek appearance and versatility make it ideal for various construction proj...
Manufacturer:
ArcelorMittal Europe Œ Long Products Œ Sections
Group:
Country of production:
Product name:
Recycled structural steel section made via EAF route made with reneweable electricity supply
Commercial names:
XCarb®
Category:
Steel and other metals
Class:
Structural steel and steel profiles
Type:
Sections
Environmental impacts
Global Warming Potential (A1-A3):
0.397 kg CO2e/kg
Technical specification:
7850 kg/m³
Available units for calculation:
kg, ton
Unique identifier (OCLID):
659affbc5e394b406603fbc9
Sustainability data background information
EPD number:
1.1.00435.2023
EPD program:
MRPI
Publication year:
2023
Product Category Rules (PCR):
EN 15804+A1, EN 15804+A2
Environmental standard:
EN15804+A1, EN15804+A2
Data source:
EPD XCarb® Recycled and renewably produced structural steel sections and merchant bars
Verification status:
Recycled
Upstream database:
ecoinvent